What is plywood?
Plywood is an engineered wood. That means it is a man-made product created by gluing layers of wood together. Plywood is extremely strong making it a wonderful construction material that resists chipping or warping, even when wet. Because of this, it is popular for all kinds of DIY and renovation projects as well as construction projects and even ship building.
The history of plywood is a little unclear. It is said that the ancient Egyptians and Greeks learned to glue thin wood together at perpendicular angles to make it stronger, while throughout the 17th and 18th centuries, veneers (layers of hard wood used to cover furniture) became popular in high class homes. Pulling these ideas together, a British naval engineer talked of laminating, or gluing, several layers of veneers in the late 19th century. But it wasn’t until the early 1900s, when synthetic glues were invented, that the waterproof, versatile, plywood as we know it, could be created.
This exhibition at the V&A showed off many of the modern day uses of this wonder wood.
How is plywood made?
Plywood can be made from soft woods such as pine or cedar, or hard woods like teak and birch. When hard woods are used, the resultant plywood will be stronger and harder wearing. In fact, plywood comes in five grades that refer to the appearance, quality and strength of the wood.
Selecting the wood
In many cases, trees are grown specifically for the purpose of making plywood and tend to be smaller in diameter than trees used to make lumbar. These trees are felled and stored ready for use.
Cutting and prepping
The first stage of plywood manufacture is to prepare the logs, this is done using machines that remove the bark using grinding wheels before sawing them into sections. The wood is then soaked and heated before lathes are used to peel off sheets of veneer. These are dried and then graded ready for the next stage.
Forming the plywood sheets
The layers of wood are glued together either manually or using a machine to spread the adhesive across the face of each veneer. Importantly the grain of each piece of wood is laid at right angles to the previous one to create rigidity and strength. The thickness of the required product will determine how many ‘layers’ are used.
The glued sheets are loaded into presses where they are both heated and ‘squeezed’ to ensure maximum possible strength. Finally, the panels are cut to the correct size and sanded to create a beautiful finish.
Why is plywood so perfect for kitchens?
As one of the most used rooms of your house, your kitchen needs to work hard for you, coping with daily cooking, cleaning and entertaining. One of the biggest reasons that kitchen units begin to fail is their exposure to damp through leakage or spillage around the sink, so choosing a material that won’t become warped, no matter how wet it gets, is important.
Plywood will outlast many other materials, keeping its shape and maintaining strength making it a great long-term investment that can be resold or reused many years down the line.
There are health benefits too. We’ve become increasingly aware that introducing new materials, paints and adhesives into our homes can bring with them VOCs, potentially dangerous toxins that can impact on our family’s health. With our plywood kitchens you won’t need to worry about this as they’ve been tested officially to contain some of the lowest levels of VOCs on the market.
And if sustainability is important to you, farmed plywood is one of the most environmentally friendly construction materials around enabling you to create a truly sustainable kitchen.
Oh, and we think plywood is beautiful too – that’s why we created Koivu.
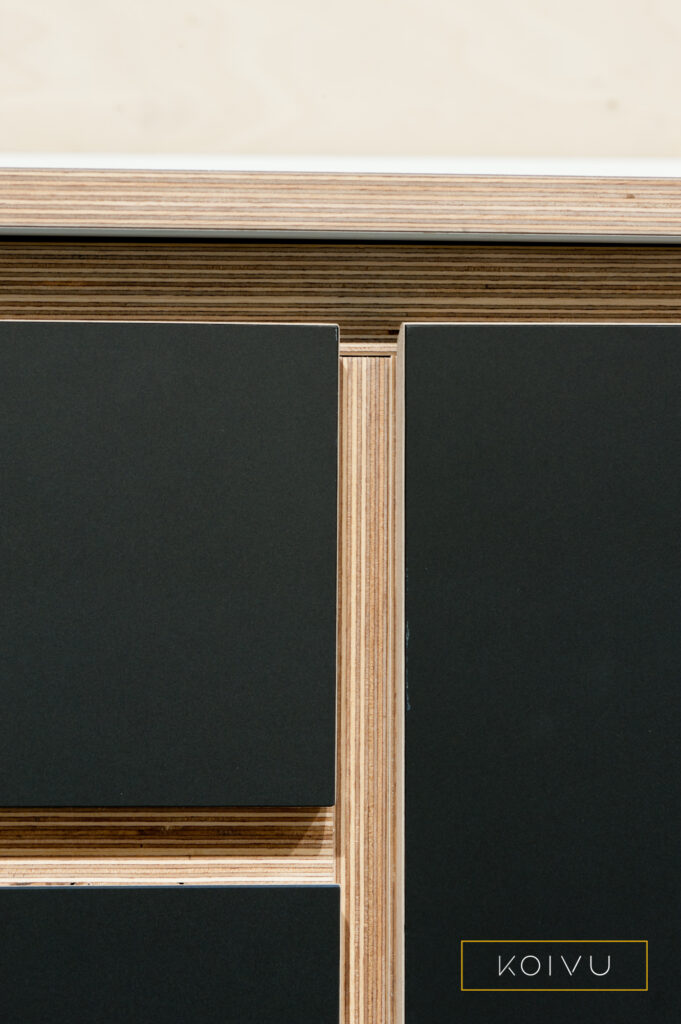
Check out some of the other reasons we love plywood and if you’d like to talk about the possibility of designing and creating a plywood kitchen of your own, why not get in contact with our talented design team.