Plotting out the journey: in the design studio
The journey starts with our designers.
When we start to work together, we’ll ask you to send us a plan of your room – usually by email as a pdf. We’ll also send you a link to complete our Kitchen Checklist – an online questionnaire. Once you’ve completed both of these, one of our friendly designers will contact you to arrange your personal consultation.
This will involve them asking lots of questions to really get to the bottom of how you use your kitchen, and your thoughts and feelings about what you want from your new design. They’ll also make helpful suggestions – sometimes things you hadn’t even thought of.
Once our designers have all the info they need, they’ll go away and come up with some plans for you. These will be sent over for your review, and no doubt we’ll go back and forth a few times working out the details.
If you would like to see a Koivu Kitchen in real life, you are always welcome to visit our showroom in Kent. Simply get in touch to book an appointment.
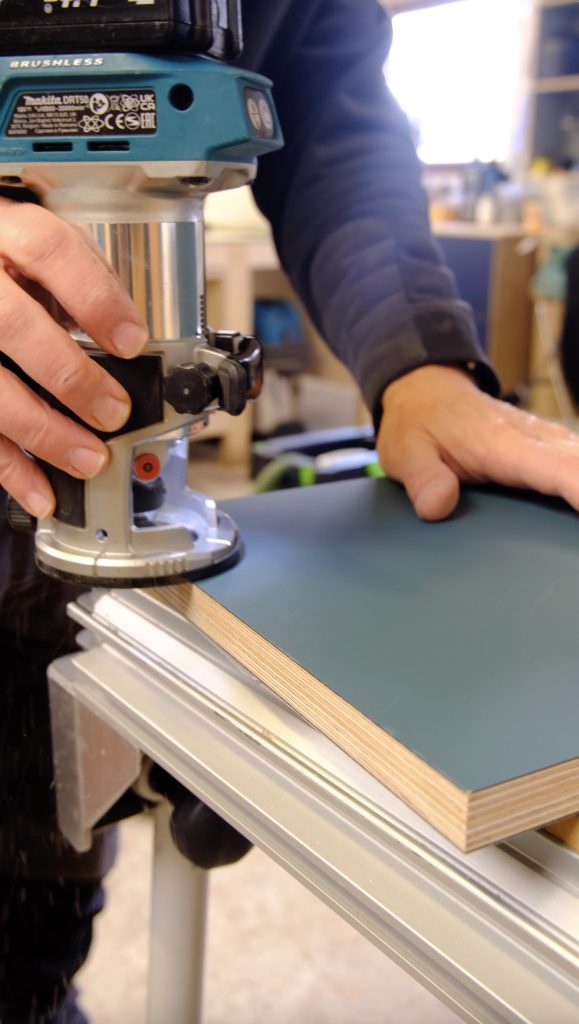
Delays en route: what if you don’t want your kitchen delivered immediately?
As part of the design process we will talk to you about your project and when you might be ready to receive your kitchen. For many of our customers the kitchen fitting is part of a much larger extension or renovation project.
As a guide, we estimate up to 12 weeks for production. But depending on your project timelines we’ll be happy to work around you. We’ll estimate a delivery date at the point you pay the deposit. Then we’ll confirm nearer the time that you will be ready for delivery. If your plans get delayed, as larger builds inevitably do, it’s no problem.
We’ll be happy to store your kitchen in our workshop until you’re ready for it and we will liaise with you to find a suitable alternative fitting date.
Next stop, workshop!
Ordering and preparing the materials
Once we have firm plans, we’ll arrange the parts we need.
The carcasses will be ordered bespoke from our long-term partner factory in Essex. Once these arrive in the workshop, they are checked, lovingly sanded down and finished with oil. Similarly, the doors will be ordered cut-to-size, and prepared with your desired laminate or veneer. Again, these are carefully checked and finished with a thorough sanding and oiling.
We do not hold stock, due to the size of our workshop, so your kitchen will always be made-to-measure at the point of order. And because we, personally, check every inch of every carcass and door, you can be sure that the final kitchen will be absolutely perfect.
Building the kitchen
Once we have received and prepared all of the individual parts, Doug and the team will carefully put them together, fitting the highest quality drawer runners, hinges and inners, and crafting handle grooves etc., where required.
Once each individual unit is made, we assemble the entire kitchen at the workshop to ensure everything is in place. We check against the original plans to reduce the risk of any nasty surprises when the kitchen gets onsite. Then we go through a standard checklist for each kitchen. Triple checking everything, so you can rest assured that all the I’s are dotted and T’s crossed before it leaves our workshop.
Finally, each unit is wrapped individually, using sustainable materials where possible, then loaded carefully onto a delivery van. Always under our watchful eye.
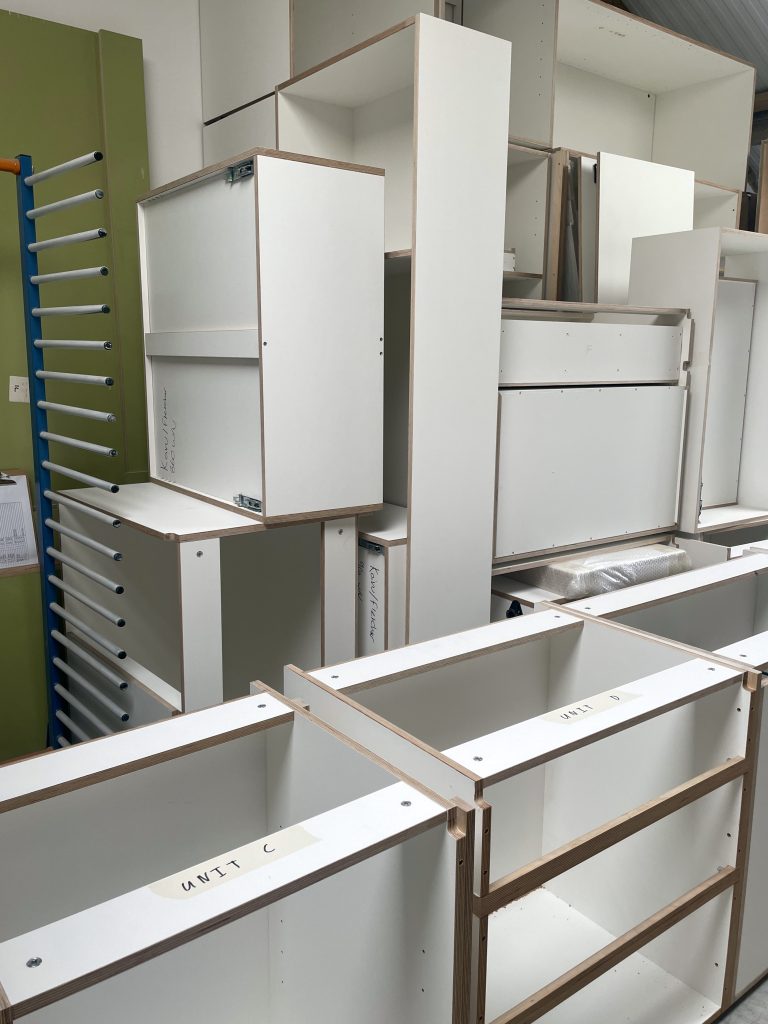
Security checkpoints: how do we guarantee high quality craftsmanship?
Hugely experienced, Douglas has worked in the kitchen industry for nearly 30 years, designing and building bespoke kitchens. In 2017, when he recognised the beauty and sustainability of plywood, he decided to specialise. Thus, Koivu was born and we have since lived and breathed plywood as our material of choice. In fact, Doug oversees the preparation of every kitchen personally.
All our processes are designed to ensure that each piece of wood used, and each element of every kitchen, is as perfect as possible, with any issues picked up at the earliest stage. As a smaller kitchen company, competing with large, well-known names, we pride ourselves on the quality of our craftsmanship. It’s one of the things our customers comment on time and again, and it’s brought many new customers, either through word of mouth, or having seen and experienced a Koivu kitchen ‘in the wild’.
And we are always looking for ways to improve. We started Koivu with the intention of using only the best materials, and in terms of both beauty, effectiveness and levels of VOCs there is very little we can improve on here. That said, we keep up to date with current trends when it comes to mechanisms or storage solutions, and are always open to suggestions from customers.
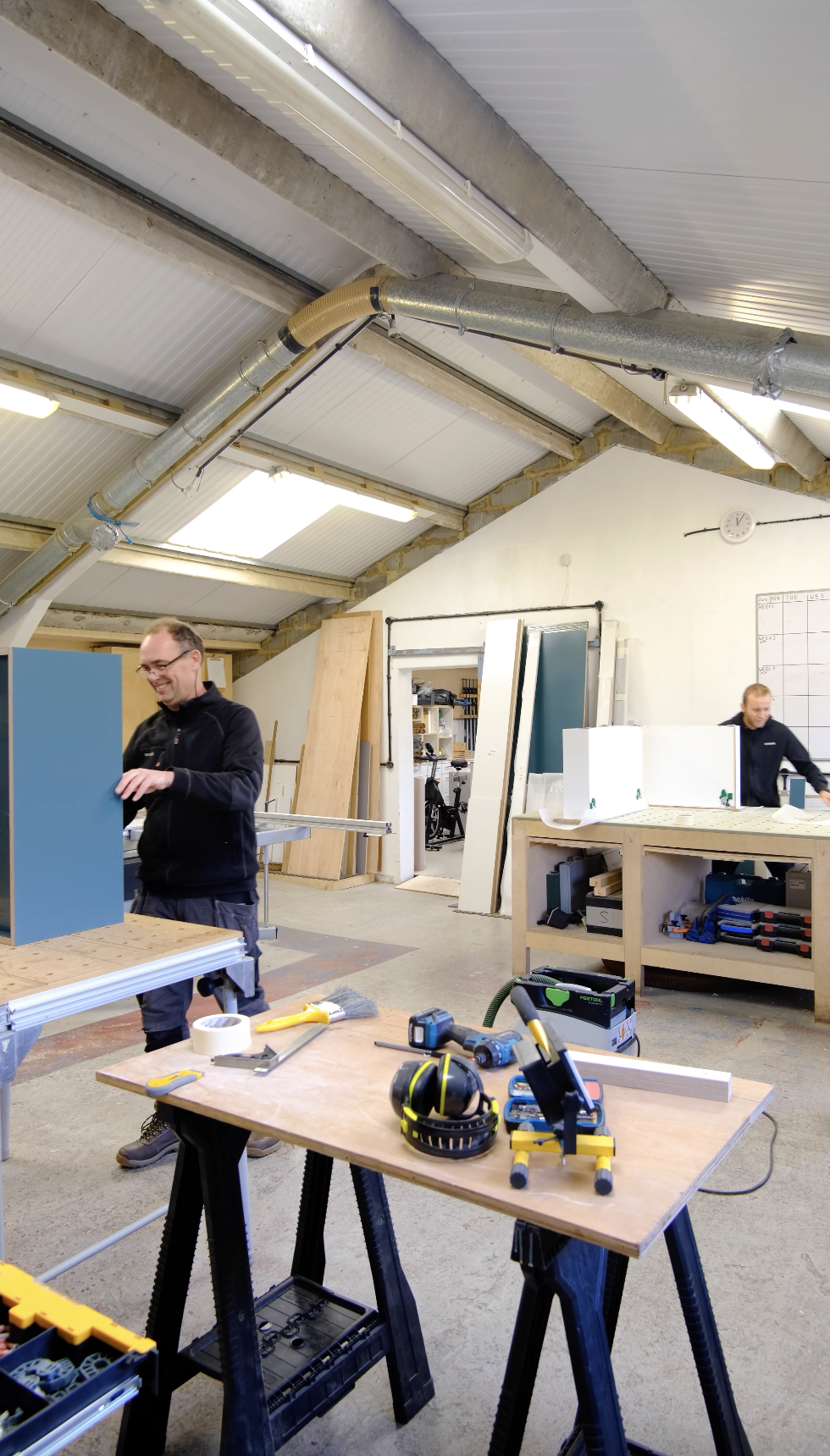
Final destination: what happens once the kitchen reaches your home?
We try to make it as easy as possible for our kitchens to be fitted quickly and efficiently by any kitchen fitter. But there’s no getting away from the fact that for the easiest option and 100% satisfaction guaranteed, it pays to opt for a Koivu fit. Apart from the fact we’re more experienced than a lot of kitchen fitters around, Doug will know your kitchen back to front so will be able to deal with any unexpected surprises.
Because we pre-fit in our workshop and ship fully assembled, most of our kitchens only take around 2-4 days to fit onsite, depending on size. Of course, if you’ve chosen your own fitter, we’ll support them to resolve anything that comes up. And in the worst case we can arrange to travel to site, for a small cost, to support the installation if it becomes necessary.
Remember it can take up to 2 additional weeks for templating and workshop fitting depending on the material and supplier you choose. But we can supply temporary worktops if necessary.
What measures do we take to minimise waste and reduce environmental impact during production and delivery?
We talk often of our commitment to sustainability and our careful choice of materials, but we also make sure our actions speak to this ethos too.
By building everything to measure we ensure all the pieces needed for the build are cut to size, resulting in little waste. While any off-cuts we do get are earmarked for smaller items such as drawers or shelves.
We are mindful of air pollution in our workshop, using good extraction to minimise dust. And these ‘nasties’ in the air are further reduced by the fact that the plywood we use is proven to have some of the lowest levels of VOCs on the market.
We choose recyclable packaging wherever possible, but there are certain places that we cannot avoid a little plastic wrap in order to ensure the kitchen reaches you in perfect condition.
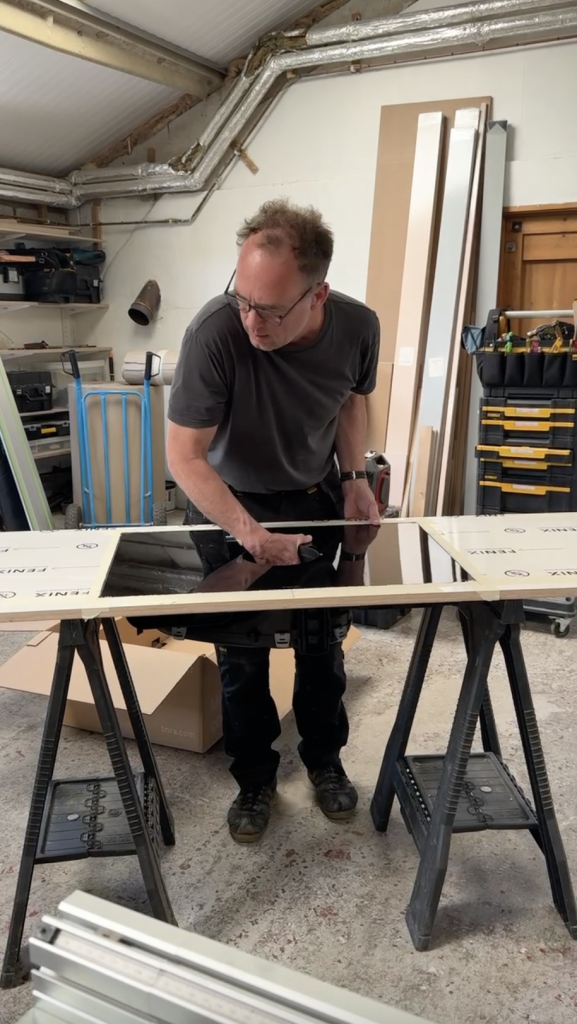
Want to start your own Koivu journey? Get in touch to ask any questions, arrange a visit to our showroom or to order your Koivu samples.